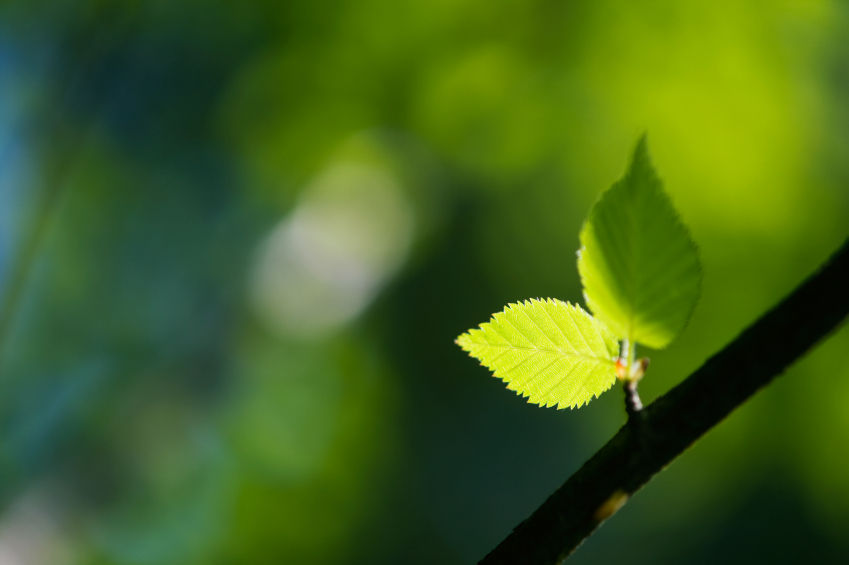
AERC Recycling Solutions
Universal Waste | Secure Data Management | End-of-Life Electronics

LSS1 Lamp Recycling Equipment
This dry-processing system crushes and separates all geometric shapes of fluorescent lamps into their components: glass, aluminum, and mercury-containing phosphor powder. The Model LSS1 provides flexible and low-cost processing with the capacity for over 3,000 lamps per hour.
The Model LSS1 also uses air pressure and built-in HEPA and carbon filters to ensure that exhaust gases are free of mercury vapor during processing.
The Model LSS1 is environmentally efficient and energy-saving solution to recycling mercury-containing lamps.
We accept many type of lamps, including traditional straight, U-shaped and coated fluorescents, as well as mercury vapor, high-pressure sodium, metal-halide, ultraviolet, ARC, and compact fluorescent and HID lamps.
Lamp Recycling.

Fluorescent Lamp Processing Explained.
FLUORESCENT LAMP RECYCLING
This operation involves processing and physical separation of fluorescent lamps containing mercury. The lamps will be separated into the streams of fluorescent lamps end caps, clean glass, phosphor powder, and, eventually, elemental mercury.
The source of these spent fluorescent lamps include households, schools, commercial and industrial sites, and the manufacturers of these lighting components. Fluorescent lamps will be transported to the facility in accordance with local, state, and federal regulations. The containers will then be off-loaded from the vehicles and stages prior to processing.
After temporary storage, the lamps will be processed in the equipment and physically separated into the components mentioned earlier. The equipment consists of a crusher, separator, particle and vapor filtration systems, material handling systems, and a program logic control system. The resulting materials generated from this activity (end caps, glass, phosphor powder) are transported off site for further processing, recycling, or disposal.
Crush and Separation
Lamp glass is broken and crushed by rotating drums and moved to a trommel system, which also separates each component and deposits it into a container. End caps are collected, sampled, analyzed for mercury content, and shipped to an off-site metals recycling facility for their aluminum content.
Glass is sampled and analyzed for mercury and sent for recycling or disposal, depending on the current market. The phosphor powder is separated for glass fines and collected in containers and shipped off-site for retort. The ferrous filaments of the lamps are removed by a magnetic separator and sent for retort.
The mercury recovered from the retorted co-products is triple distilled and sold on the domestic market as Technically Pure Mercury.
An industrial blower maintains negative pressure across the entire lamp processing system, drawing air through the system to clean off residual dust and powder with a series of nine baghouse cartridge filters. These filters are automatically flushed to prevent powder build-up, and air passes through a carbon filtration system prior to discharge.
Thermal Recovery Unit
The powder separated by the LSS1 is fed into the retort unit where, through the application of heat, the mercury vaporizes, and then condenses into liquid form. This commodities-grade mercury is collected for the Triple Distillation Process.
Triple Distillation Process
Retorted mercury is distilled three times to remove impurities. When the Triple Distillation Process is complete, the mercury is analyzed by an independent metallurgical laboratory for appearance and certification that it is at least 99.99 percent pure. Upon verification of purity, the Technically Pure Mercury product is packaged according to individual customer specifications and sold to companies that manufacture mercury salts, mercury-containing devices, or utilize mercury in electronics and various research and development applications.
HID Lamp Processing Explained.
Component Separation
Under a negative airflow, the outer globe of glass is removed from the base and metal stem of the lamp which houses the inner arc tube. The inner arc tube is made of quartz glass and contains mercury.
The non-mercury bearing parts are separated, sorted by material type, tested for mercury contamination and then sent out for further recycling. The inner arc tube which contains mercury is breached and placed into a retort for additional processing.
Retort
The inner arc tubes are place into a retort oven where the glass is heated to a high temperature which causes the mercury to evaporate off the glass. The mercury is then cooled, collected and held for additional processing. The inner arc tubes, which are now clean, are also cooled, sampled and sent out for recycling.
Triple Distillation Process
The crude grade mercury recovered from the thermal process is distilled three times to remove impurities, turning the mercury into a product grade metal.

Using our RecycleKits is a great way to ensure proper packaging and processing of lamps for recycling!